Manufacturing Overview
United is a company built on manufacturing quality where every major component is manufactured and custom fitted to that particular machine. Manufacturing quality is a keystone of the United operation and in their manufacturing facility there is a combined expertise of over 150 years. Component tolerances are at the extreme minimum where the slightest error can result in wasted effort and a ruined component. As each component proceeds through its manufacturing phase it is measured, tested, finished, re-measured and re-tested. Nothing is left to guesswork or chance. Every single component with the exception of the drive motors and electronic controls are manufactured by United using only those materials that best combat fatigue and provide the durability to withstand the kind of high speed heat and pressures that can be encountered during use. The pride and care taken in the manufacturing plant becomes evident in the overall quality of the finished product.
Private Label Manufacturing
United’s centrifuges are known industry wide for their rugged reliability, ease of service, ease of operation and user friendliness. As such they are frequently manufactured for re-branding and used as product representative of other centrifuging companies for their product or industry-specific applications. United is proud to have their centrifuges selected as the product of choice for some of the leading companies in a variety of industries.
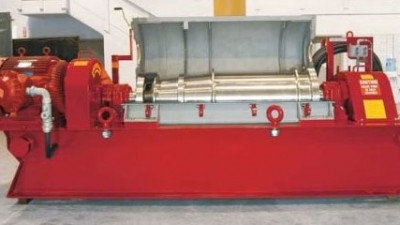
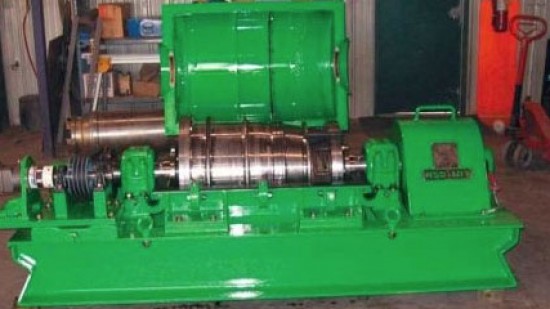
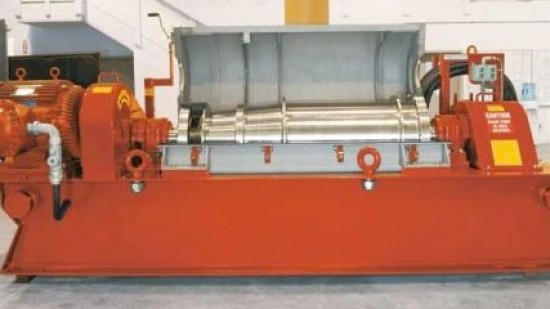
Centrifuge Assembly
By the time the skid arrives at the assembly point, all component parts have been collected. Assembly and testing is the final part of the operation and the last opportunity to ensure that the quality going out the door lives up to the expressed standards of the company and its product warranty. As mentioned previously, each component is custom fitted and the assembly of any of the three centrifuges can take up to 8 hours or more. The first thing that is attached is the motor. Special electrical cabling is required for operation and it too is installed. When the auger and bowl arrive the two are fitted together and sealed. The gearbox is balanced, attached and the entire rotating assembly is sent for balancing as a combined unit. The balancing machine works on the same principle as that used for car tires –weight is added or taken away in various increments according to electronic measurements. After the rotating assembly is balanced, the case is installed into the skid housing, and the rotating assembly is installed into the case. Drive belts are attached and safety guards are installed over the moving parts. At each process along the way, the various parts are fitted and tested for tolerances. When the operation is complete, the unit is tested again and made ready for shipment
Rotating Assembly
The double planetary gear-box, stainless steel auger and bowl which form the rotating assembly, and the stainless steel case that provides operational containment are all finished and assembled on the production floor of the main plant. The auger, its flighting and feed chamber require the utmost attention due to design and operating complexity. Once the flight blades have been welded into position, blades are machined and tiled using tungsten carbide. The auger is then finely balanced to optimize efficiency and ensure trouble-free operation. Rotating assemblies are manufactured from 304L or 316L stainless steel but can also be manufactured from mild steel when applications are less corrosive. Bowl and auger undergo stress relief prior to assembly. Rotating assemblies are also machined and balanced to withstand high speed pressures. Prior to delivery, each centrifuge is performance tested.
Containment Case
The case is fabricated, fitted and finished to the dimensions of the machine using 1/4" thick stainless steel plate with high wear areas plated to 1/2" thickness and hard surfaced for extra durability.