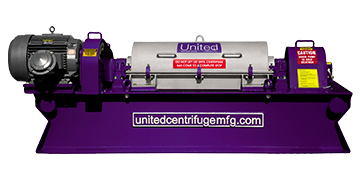
SS1000 LHF-HP
(Available in Back-Drive)
The SS1000 LHF-HP is United’s newest addition to its product line of centrifuges. The LHF-HP promises high speed and high performance – specifically designed for those industries that require a greater degree in the separation of low gravity solids.
The LHF-HP processes feed slurries of solids and liquids up to 1,000 liters/min.
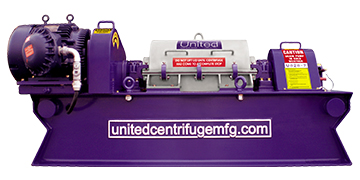
SS800
Of the three high speed / high volume decanting centrifuges that United manufactures, the smallest unit is the SS800.
The SS800 is primarily for use in the environmental waste management industry but has found applications in many other areas as well. It is capable of processing 800 liters/min of feed slurries of solids and liquids. Ideal for heavy solids.
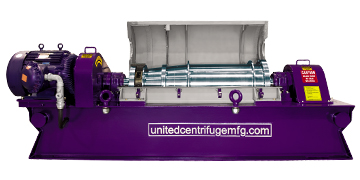
SS2000
(Available in Back-Drive)
The SS2000 is for high volume. Its processing capacity is greater than TWO – SS1000 LHF-HP's combined … but is ideal for conditions where a high volume processing capacity is needed … but a smaller footprint is required! The SS2000 is currently the largest centrifuge in United's product line. This unit is recommended for heavy industrial operations where applications might require consistently high processed volumes. Process rated to 2,000 liters/min of feed slurries of solids and liquids.
United Centrifuge MFG manufactures 3 models of high speed, horizontal decanting, 2 phase centrifuges that separate solids from liquids. In all three models, the operating principle is theoretically the same.
There are 3 primary parts - the base, or skid – the stainless steel case – and the rotating assembly consisting of bowl and auger. The case gathers the separated materials in two chambers for re-use and disposal. To create the desired effect, bowl and auger spin at slightly different speeds in the same direction. Bowl speed is variable depending on application and operating conditions.
During operation, feed slurry is dispersed in the feed chamber of the auger. The slurry strikes an accelerator plate and is forced into the bowl. Centrifugal force causes heavier solids to accumulate inside the bowl while the auger continuously drags them up the taper end of the bowl and out of the solids discharge ports. Finer solids, retained in the liquid traveling through the machine, are continuously removed as they buildup inside the bowl, and are ultimately augered along the pool, up the taper and out the solids discharge ports.
Clean fluids travel towards the fluid end of the bowl, exit through adjustable eccentric ports and are recycled back into the operation system or re-directed to another location for storage or removal.
Applications
Although all three centrifuges have been used extensively in the oilfields of the world, recently, the company has broken new ground in other types of process industries where the separation of solids and liquids is required. Rendering, waste control, environmental cleanup and others have all found United's centrifuges more than capable of providing what they need. And because of this kind of customer-base-expansion, the Company has opened service and parts centers in Canada and the USA.
Rendering
Lagoon Waste
Blood Meal
United's premium quality tungsten carbide tiles are designed to protect against excessive conveyor wear in highly abrasive processes. The tile was specifically designed for installation on horizontal decanting centrifuge conveyors and can be installed in most brands of horizontal decanting centrifuges with bowl diameters up to 24 inches and 36 inches.
United's tiles uses a sintered sub-micron tungsten carbide material. These tiles have been installed on various types of machines and have performed successfully in many different applications. Conveyor contact surfaces fitted with United's Tungsten Carbide Tiles are up to 50 times more resistant to wear than surfaces treated with other materials.
Up to 24 inch Diameters
United's premium quality tungsten carbide tiles are designed to protect against excessive conveyor wear in highly abrasive processes. The tile was specifically designed for installation on horizontal decanting centrifuge conveyors and can be installed in most brands of horizontal decanting centrifuges with bowl diameters up to 24 inches.
United's tiles uses a sintered sub-micron tungsten carbide material. These tiles have been installed on various types of machines and have performed successfully in many different applications. Conveyor contact surfaces fitted with United's Tungsten Carbide Tiles are up to 50 times more resistant to wear than surfaces treated with other materials.
Up to 36 inch Diameters
United's premium quality tungsten carbide tiles are designed to protect against excessive conveyor wear in highly abrasive processes. The tile was specifically designed for installation on horizontal decanting centrifuge conveyors and can be installed in most brands of horizontal decanting centrifuges with bowl diameters up to 36 inches.
United's tiles uses a sintered sub-micron tungsten carbide material. These tiles have been installed on various types of machines and have performed successfully in many different applications. Conveyor contact surfaces fitted with United's Tungsten Carbide Tiles are up to 50 times more resistant to wear than surfaces treated with other materials.